Printing Techniques: Coatings
Are they right for your brand image?
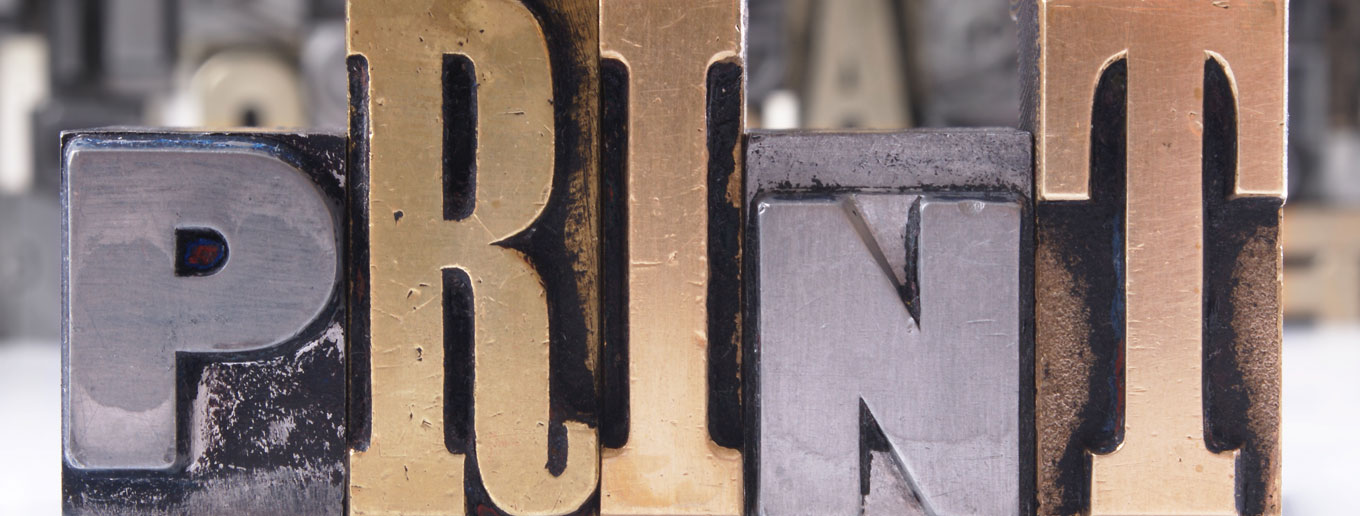
Many unique printing techniques are available today that can enhance your brand image. This is the first in a four-part series all about these processes and about when it makes sense to splurge on them.
Why use alternative printing techniques and when to use them?
Are they really necessary? Necessary, no, but if you want to stand out from the crowd and make a statement about your brand, they can be useful. If you look at all of the touchpoints you share with your customers, some are more important than others. Focus on making the ones that are key to your sales process—the ones at key points in the decision making process—as special as you can make them.
What is standard printing?
Usually, “standard printing” means offset. However, in the last 10 years or so, digital printing has overtaken traditional offset printing, particularly for small runs. For more detail on the difference, read this article.
Printing can be purchased online or from a local vendor, and different sources provide a wide variety in regard to the level of service and quality. Choose a resource that best fits your needs for cost, ability, and attentiveness.
Why use a coating?
Today we are going to focus on coatings. These are all available with offset printing and many are also available on digital presses. Check with your printer to see what they offer. There are several reasons why you would choose to add a coating to your printed piece:
Protection—A coating can add a layer of protection to printing. It can help prevent the ink from rubbing off on to the surface next to it, such as pages in a book or a stack of business cards in a box. A heavier coating, such as lamination can prevent tears. If your collateral is going through the mail or spending a lot of time in suitcases with a traveling sales force, this is important.
Visual interest—By varying gloss and dull coatings, you can add visual interest to your collateral that is subtle and sophisticated.
Readability—By adding a dull coating you can reduce glare and make text more readable.
What are the different types of coating?
Here's four common types of coating and reasons why it might be the right choice for your project.
Varnish—Varnish is probably the most common coating used. It is a clear liquid that is applied to paper on press in a similar fashion to ink. It is available in gloss, matte, and silk finishes. An all-over varnish is used on many designs just for a layer of protection to avoid ink rubbing off. A spot varnish can be used to highlight certain areas of a design. Because varnish goes on just like ink, any shape can be created for that layer. The effects of dull and gloss varnish will be most apparent on coated paper. It is very difficult to see any difference on an uncoated sheet.
Dry trapping is another technique that enhances the difference between gloss and dull varnish. The piece is run through the printer without varnish, allowed to dry, and then run through again to add the varnish. This, of course, takes more time and labor so the cost goes up.
The benefits of varnish are that you can make any shape you want, it offers a fairly good level of protection, and it is the least expensive of any coating. The downside is that it takes up one unit of ink in the press. Depending on your print resource, this may be an issue of cost or timing. Additionally, it is slow to dry, it can cause some environmental issues because of off-gassing, and it tends to yellow over time.
UV Coating—UV coating is a liquid that is cured on press with an ultraviolet light. Because of the curing process, it is dry by the time it comes off press. The result is a very high gloss finish. It can also be done in any shape desired. Drawbacks are that it can be hard to write or imprint on any surface that has been UV coated and the shiny surface may not be right for all projects. It is best on heavier weight paper.
Aqueous—Aqueous, as its name suggests, is a water-based coating. It is, like varnish, available in gloss and matte finishes, but unlike varnish it must be applied over an entire page. It dries very quickly so there is usually no wait time to cut, fold, or bind after printing.
It is more environmentally friendly than varnish and it resists yellowing. It also provides more scuff resistance. The downside is it costs about twice what varnish does.
Lamination—Lamination is the most sturdy of the coating options. It can even make a sheet waterproof if used on both sides and sealed. It is applied as a film or a liquid (depending on the style) as a separate process from printing. This adds to both cost and timing. It is available in gloss or matte finishes and must cover the whole page.
Lamination does not work well on heavily textured sheets and heavier laminates cannot be recycled. Also, high gloss finishes can make text harder to read.
The bottom line is you have to assess the needs of each project and choose the right coating (or no coating) for the job. Look for more articles to come about unique printing techniques such as ink alternatives, processes that modify paper, and different substrates.
Offset vs. Digital Printing
How to know which is best.
Printing Techniques: Modifying the Paper
Modify the paper on printing jobs to add impact.
Printing Techniques: Using Different Substrates
Printing doesn’t always have to be on paper.